Keeping Time Industrial-Style at
Lockerbie & Hole
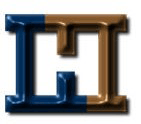
"...up to seven hours to run a report. Now, on a job the same size, we’re running reports out of TimeControl in a matter of minutes.”
Monica Panas, Business Intelligence Analyst
For more than 100 years, Lockerbie & Hole has been helping to “build” Canada. Founded as a plumbing firm in 1898, today the company is one of the country’s largest, full-service, multi-trade, industrial process contractors. Its team of experienced construction professionals provides piping, electrical, mechanical, instrumentation and fabrication services to the automotive, steel, petrochemical, mining, pulp and paper, oil and gas, and food and beverage sectors.
Not only has the scope of the company’s work grown more complex over the course of a century, but client expectations have also become much more sophisticated, says Lockerbie & Hole Business Intelligence Analyst Monica Panas. “When I started working in the construction industry over 20 years ago, it was so simple,” says Panas. “Now it’s getting more and more complicated; our client demands are very specific and we’re required to meet them.”
For large industrial clients, including Syncrude Canada, Suncor and Shell Canada, Lockerbie & Hole must provide daily reports that track labor, equipment and material for billing purposes. With anywhere from 1,500 to 4,000 contract employees working at any given time on projects located across the country, collecting the required information can prove challenging – especially when the bulk of the workforce is out in the field.
Up until 2004, Lockerbie & Hole relied on an off-site time capture system to help gather the necessary data. When that system became obsolete, it needed to find a replacement quickly. On the advice of an external consultant, the company selected TimeControl from Montreal-based HMS Software, an electronic timesheet system that integrates with both finance and project management systems.
TimeControl closely matched the functionality required by Lockerbie & Hole, says Panas, and it was the willingness of HMS to add some features specific to industrial contracting that helped clinch the deal. In particular, Lockerbie & Hole needed to enter time for an entire construction crew at once as opposed to individually, handle complex billing rates associated with unionized labourers, comply with new privacy legislation pertaining to the handling of personal information, and track multiple resources.
“We have extensive experience in the Heavy Industry sector,” says HMS President Chris Vandersluis. “With Lockerbie and Hole we saw an opportunity to tailor our timesheet to the needs of a specific client and to help make their operations more efficient.”
In the case of Lockerbie & Hole, this meant adding features like a crew entry interface that handles crew-based timekeeping, a billing table that maintains union rates by job category, and a module that monitors material usage.
HMS has now made many of these changes available commercially as part of TimeControl Industrial, a release of TimeControl targeted at industries where organizations need to track the labour hours of both the back office and field personnel.
Stephen Eyton-Jones, HMS Software Director of Technical Services, was instrumental in the Lockerbie & Hole TimeControl development and considers them a launch client for TimeControl Industrial. “Much of the work we did for the Lockerbie and Hole deployment of TimeControl helped guide our thinking towards what would be an effective industrial version of our product,” he says.
Vandersluis points out that many businesses view timesheet collection as a simple business process. While he concedes the data entry process should be simple, what happens to the information afterwards is often very complex. At Lockerbie & Hole, for example, timesheet data once entered becomes part of an integrated process that serves billing, human resources, productivity reporting, profitability and overall advancement of the project plan.
Each Lockerbie & Hole job site is assigned a TimeControl administrator who is responsible for collecting construction crew data from the foreman, keying it into TimeControl and maintaining the system in order to ensure client reporting requirements are met. The software is deployed on Windows-based PCs using a thin client computing model, and the TimeControl database is maintained on a corporate Microsoft SQL server at the company’s head office location in Edmonton.
According to Panas, the flexibility of TimeControl is a huge benefit. “Our time entry data isn’t just used to pay people; we leverage it into a number of different areas,” she says, noting that payroll data is automatically exported from TimeControl into the corporate payroll system, alleviating clerks from the mundane task of manual entry. Conversely, union rates for each type of pay code, such as regular time, overtime, double time, leave, travel time and meals, are automatically brought into TimeControl to ensure the correct rates are associated with labourers according to their classifications.
Recently, Lockerbie & Hole integrated TimeControl with an in-house productivity reporting tool that combines quantity of work completed with budgeted hours and actual hours in order to provide what Panas calls “true percent completion” of a project. Every night, data is pulled from the various environments in the field and consolidated onto a central data repository to produce weekly productivity reports, using standard cost codes.
“You can’t just say that out of our budget of 10 hours we’ve spent nine, so that means we’re 90 percent complete; that’s not going to work,” she explains. “You actually have to have quantity in there as well, as in ‘we laid so many linear feet of pipe,’ in order to get true productivity factoring.”
The daily reporting that Lockerbie and Hole now generates from TimeControl puts them at the forefront of effective Business Intelligence Analysis in their industry. Managers are now able to react to changes within hours instead of days. This provides a degree of manoeuvrability to the company that is essential in today’s economy.
Time entry data from TimeControl is also integrated with other corporate data marts, including Lockerbie & Hole’s business intelligence software from Ottawa-based Cognos Inc. Using the Cognos Impromptu product, for example, Panas has created a standard set of reports based on information stored in the TimeControl database.
“The most important advantage for analysis and reporting is that TimeControl uses an open database structure, whereas our old time capture system was proprietary. On a big job site, it used to take up to seven hours to run a report. Now, on a job the same size, we’re running reports out of TimeControl in a matter of minutes.”
Monica Panas, Business Intelligence Analyst
Panas refers to TimeControl as a “heads up” timekeeping system, meaning the people who are entering the data need to understand the information they’re keying and know when to ask for clarification. As a result, her confidence level in the accuracy of the data coming out of the system is extremely high, she says.
Looking forward, Lockerbie & Hole plans to integrate TimeControl with its project scheduling software, and also intends to migrate to TimeControl Industrial.
“Working with HMS has been a very positive experience,” says Panas, who says she’s pleased to see some of her company’s recommendations available as standard features in the industrial version of TimeControl. “Supplying accurate, meaningful information to our owners and clients every day is paramount and TimeControl is exactly what we needed to fit the bill,” she says.